多層板電阻點銲
由於全球暖化與能源危機問題日趨嚴重,因此提高燃油效率、降低燃油消耗及減少廢氣排放已成為國際汽車製造廠首要任務。根據文獻指出,當車身減重10%時,除了將提高約5.5%燃油效率外,亦將降低約6~8%燃油消耗,且減少約4.5%廢氣排放。另當發生交通事故時,車體結構需能確保駕駛與乘客安全,藉以降低因事故而造成人員死傷。有鑑於此,國際汽車製造廠大量採用先進高強度鋼製造車體結構,藉以兼顧車身輕量化與駕乘安全性。先進高強度鋼儼然成為車體結構製造的首選材料。針對先進高強度鋼工頻交流點銲,銲核於先進高強度鋼材性質影響,傳統軟鋼或普通高強度鋼可忽略之缺陷效應將相對放大,使得先進高強度鋼銲後易發生搭接強度不良缺失。當採用多層金屬板件與車身剛性升級之設計理念生產製造車體結構時,將可大幅強化駕乘人員的安全防護,然多層板件係電阻點銲中技術難度最高之搭接方式。早期電阻點銲研究偏重於相同材質與厚度之二層板件搭接,參數調控僅需考量電極挾持力、銲接電流及銲接時間。然進行多層板件電阻點銲,除了需精準調控點銲三大製程參數外,另需考量多層板件搭接厚度比。此外,由於多層板件搭接總厚度一般皆大於4 mm,因此銲核容易產生中心縮孔或熔融不良瑕疵。研發團隊除了成功研發多層板件電阻點銲技術外,亦已建置先進高強度鋼電阻點銲參數資料庫。本創新技術(已取得臺灣發明專利)除了可提高多層先進高強度鋼板電阻點銲品質外,亦可發揮節約電力能源功效。本成果榮獲科技部工程司106年度產學合作計畫『產學成果簡報特優獎』。
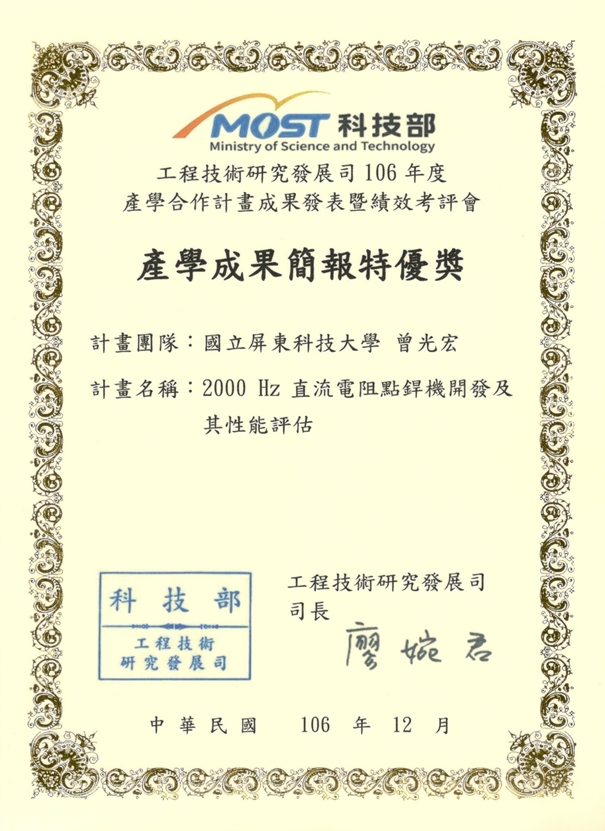